QR Code
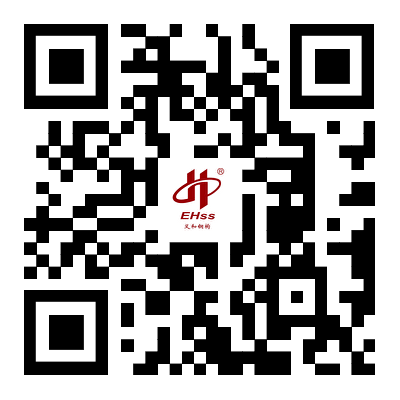
Products
Contact Us
Phone
E-mail
Address
No. 568, Yanqing First Class Road, Jimo High-tech Zone, Qingdao City, Shandong Province, China
Steel structure engineering building is known as the green project of the 21st century, steel structure has many advantages such as high strength, strong loading capacity, light weight, small volume of space occupied, easy manufacture and installation of components, saving wood, etc., so it is more and more widely used in industrial and civil buildings.Steel Frame Buildings and Steel Structure Warehouses are everywhere.
With the rapid development of industry, steel corrosion resistance and poor resistance to rust and corrosion and other issues gradually appeared, especially in coastal areas and the chemical industry has become a prominent problem!
Corrosion of steel structure not only causes economic losses, but also brings hidden danger to the safety of the structure, and engineering accidents caused by steel corrosion are common, so the anti-corrosion treatment of steel structure (especially thin-walled steel components) is of great economic and social significance, and the following are some introductions and discussions on the problems found in the process of construction and some treatment methods.
1. Main causes of corrosion of steel structures
Preventing steel corrosion starts with understanding the causes of steel corrosion.
1.1 Corrosion mechanism of steel at room temperature (below 100°C)
Corrosion of steel at room temperature is mainly electrochemical corrosion. Steel structures are used in the atmosphere at room temperature, and the steel is corroded by the action of moisture, oxygen and other pollutants (uncleaned welding slag, rust layer, surface dirt) in the atmosphere. The relative humidity of the atmosphere is below 60%, the corrosion of steel is very slight; but when the relative humidity increases to a certain value, the corrosion rate of steel suddenly rises, and this value is called the critical humidity. At room temperature, the general steel critical humidity of 60% to 70%.
When the air is polluted or salt in the air in coastal areas, the critical humidity are very low, the steel surface is easy to form a water film. At this time, welding slag and untreated rust layer (iron oxide) as the cathode, steel structure components (base material) as the anode in the water film electrochemical corrosion. Atmospheric moisture adsorbed on the steel surface to form a water film is the determining factor for steel corrosion; the relative humidity of the atmosphere and the content of pollutants are important factors affecting the degree of atmospheric corrosion.
1.2 Corrosion mechanism of steel at high temperature (above 100℃)
Corrosion of steel at high temperatures is mainly chemical corrosion. At high temperature, water exists in a gaseous state, the electrochemical effect is very small, reduced to a secondary factor. Metal and dry gas (such as O2, H2S, SO2, Cl2, etc.) contact, the surface generation of the corresponding compounds (chlorides, sulfides, oxides), the formation of chemical corrosion of steel.
2 Methods of protection against corrosion of steel structures
According to the electrochemical principle of steel corrosion, as long as the formation of corrosion battery is prevented or destroyed or the cathodic and anodic processes are strongly blocked, the corrosion of steel can be prevented. The use of protective layer method to prevent corrosion of steel structure is a common method at present, the commonly used protective layer has the following kinds:
2.1 Metal protective layer: metal protective layer is a metal or alloy with cathodic or anodic protective effect, through electroplating, spray plating, chemical plating, hot plating and seepage plating and other methods, the need to protect the metal surface to form a metal protective layer (film) to isolate the metal from the corrosive medium in contact with the corrosive medium, or the use of electrochemical protective effect of metal protection, so as to prevent corrosion.
2.2 Protective layer: through chemical or electrochemical methods to make the steel surface to generate a corrosion-resistant compound film, in order to isolate the corrosive medium and metal contact, to prevent corrosion of metal.
2.3 Non-metallic protective layer: with paints, plastics, enamel and other materials, through painting and spraying and other methods, to form a protective film on the surface of the metal, so that the metal and corrosive media to isolate, so as to prevent the corrosion of the metal.
3. Steel surface treatment
Steel processing to the factory before, the surface of the components will inevitably be stained with oil, moisture, dust and other pollutants, as well as the presence of burrs, iron oxide, rust layer and other surface defects. From the previous main reasons for corrosion of steel structure, we know that the content of pollutants is an important factor affecting the degree of atmospheric corrosion, and surface contaminants will seriously affect the adhesion of coatings on the surface of the steel, and make the paint film under the corrosion continues to expand, resulting in coating failure or damage, unable to achieve the desired protective effect. Therefore, the quality of steel surface treatment on the protective effect of the coating and the life of the influence, sometimes even more than the coating itself varieties of performance differences in the impact of the following aspects should be emphasized:
3.1. For the load-bearing components which are difficult to be repaired during the service period, the descaling grade should be increased appropriately.
3.2. Before and after descaling, grease, burr, medicine skin, splash and iron oxide should be carefully eliminated.
3.3. the quality acceptance of the descaling and painting works shall be in accordance with the regulations.
4.Anti-corrosion Coating
Anti-corrosion coatings are generally composed of primer and top coat. Primer in the powder more, less base material, film rough, the function of the primer is to make the paint film with the grass-roots level and the topcoat combination of solid, that is, to have a good adhesion; primer has corrosion inhibiting pigments, can prevent the occurrence of corrosion, and some can also be passivation of the metal and the electrochemical protection to prevent the metal from rusting. The topcoat is less powder, more base material, after the film is glossy, the main function is to protect the lower layer of primer, so it should be impermeable to the atmosphere and humidity, and should be able to resist the physical and chemical decomposition caused by weathering. The current trend is to use synthetic resins to improve the weathering resistance of the medium. Anti-corrosion coatings with atmospheric resistance are generally only resistant to vapor phase corrosion in the atmosphere. For places subject to corrosion by acids and alkalis and other media, acid and alkali resistant coatings must be used.
Anti-corrosion paint according to the protective function can be divided into primer, middle paint and top coat, each layer of paint has its own characteristics, each responsible for its own responsibility, the combination of the layers, the formation of a composite coating to improve anti-corrosion performance, prolong the service life.
4.1primers
Primer layer commonly used anti-corrosion coatings are zinc-rich primer and epoxy iron-red primer, zinc-rich paint is composed of a large number of micro-fine zinc powder and a small amount of film-forming materials. Zinc's electrochemical properties are higher than those of steel, and when subjected to corrosion, it has a "self-sacrificing" effect, so that the steel is protected. The corrosion product zinc oxide fills the pores and makes the coating more dense. Commonly used zinc-rich primer has the following three kinds:
(1) water glass inorganic zinc-rich primer, it is water glass as a base material, add zinc powder, mixing and brushing, after curing to be rinsed with water, the construction process is complex, harsh process conditions, the surface treatment must be in the Sa2.5 or more, in addition to the ambient temperature, humidity requirements, the formation of the coating film is easy to cracking, peeling, and has been rarely used.
(2) soluble inorganic zinc-rich primer, the primer is based on ethyl orthosilicate, alcohol as a solvent, partially hydrolyzed polymerization, add zinc powder mixed evenly coated film.
(3) zinc-rich primer, it is epoxy resin as a film-forming base material, adding zinc powder, curing to form a coating. Epoxy zinc-rich primer is not only excellent anticorrosion properties, and strong adhesion, and with the next coating epoxy iron-cloud paint are good adhesion type. Mainly used in the general atmosphere of the steel frame structure and petrochemical equipment corrosion.
Epoxy iron oxide red primer is divided into cans of two-component paint, component A (paint) made of epoxy resin, iron oxide red and other antirust pigments toughening agent, anti-sinking agent, etc., component B is a curing agent, the construction of the proportion of the deployment. Iron oxide red is a kind of physical anti-rust pigment, its nature is stable, strong covering power, fine particles, can play a good shielding effect in the paint film, has good anti-rust performance. Epoxy iron oxide red primer on the steel plate and the upper layer of epoxy paint have good adhesion, fast drying at room temperature, the upper layer of surface paint does not bleed color, more commonly used in steel pipelines, tanks, steel structure anticorrosion projects, as rust primer.
4.2 middle layer of paint
The middle layer paint is generally epoxy mica and epoxy glass scale paint or epoxy thick slurry paint. Epoxy mica paint is made of epoxy resin as base material by adding mica iron oxide, the microstructure of mica iron oxide is like flaky mica, its thickness is only a few micrometers, and its diameter is tens of micrometers to one hundred micrometers. It is high temperature resistance, alkali resistance, acid resistance, non-toxic, flake structure can prevent medium penetration, enhanced anti-corrosion performance, and low shrinkage, surface roughness, is an excellent middle layer of anti-corrosion paint. Epoxy glass scale paint is epoxy resin as the base material, with flaky glass scale as the aggregate, plus a variety of additives composed of thick paddle-type anticorrosion paint. Glass scale thickness is only 2 to 5 microns. As the scales are arranged in layers above and below in the coating, a unique shielding structure is formed.
4.3 top coat
The paints used for topcoats can be divided into three grades according to their price points:
(1) Ordinary grade is epoxy paint, chlorinated rubber paint, chlorosulphonated polyethylene its and so on;
(2) Medium grade is polyurethane paint;
(3) Higher grade is silicone-modified polyurethane paint, silicone-modified acrylic top coat, fluorine paint and so on.
Epoxy paint after chemical curing, chemical stability, dense coating, strong adhesion, high mechanical properties, it is resistant to acid, alkali, salt, can resist a variety of chemical media corrosion.
5. The selection of anticorrosive paint should consider several points
5.1 Consideration should be given to the consistency of the conditions of use of the structure and the range of paints selected, based on the corrosive medium (type, temperature and concentration) gas phase or liquid phase, hot and humid areas or dry areas and other conditions for selection. For acidic medium, phenolic resin paint with better acid resistance can be used, while for alkaline medium, epoxy resin paint with better alkali resistance should be used.
5.2 The possibilities of construction conditions are to be considered. Some are suitable for brushing, some are suitable for spraying, some are suitable for natural drying to form a film and so on. For general conditions, it is advisable to use dry, easy to spray cold-setting paint.
5.3 Consider the correct matching of coatings. As most of the paint is an organic colloidal material as the base material, paint every layer of film, there are inevitably many exceptionally small microporous, corrosive media may still penetrate the erosion of steel. Therefore, the construction of the current paint are not coated single layer, but coated multi-layer, the purpose is to reduce the microporous to a minimum. There should be good adaptability between primer and topcoat. Such as vinyl chloride paint and phosphating primer or iron red alkyd primer supporting the use of good results, and can not be used with oil-based primer (such as oil-based red paint) supporting the use. Because perchloroethylene paint contains strong solvents, will destroy the primer film.
It is of great significance to do a good job in antirust and anticorrosion to promote the development of steel structure building, save materials, extend the service life of the building, ensure safe production and reduce environmental pollution.
No. 568, Yanqing First Class Road, Jimo High-tech Zone, Qingdao City, Shandong Province, China
Copyright © 2024 Qingdao Eihe Steel Structure Group Co., Ltd. All Rights Reserved.
Links | Sitemap | RSS | XML | Privacy Policy |
Teams