QR Code
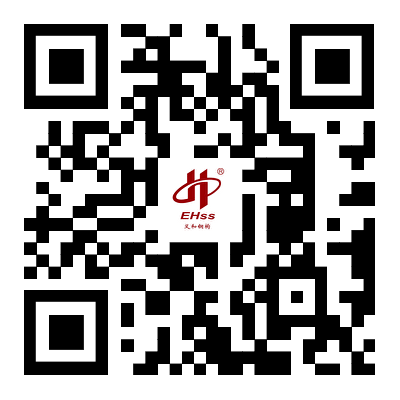
Products
Contact Us
Phone
E-mail
Address
No. 568, Yanqing First Class Road, Jimo High-tech Zone, Qingdao City, Shandong Province, China
Connections are structural elements used for joining different members of a structural steel framework. Steel Structure is an assemblage of the different members such as “Beams, Columns” which are connected to one other, usually at member ends fasteners so that it shows a single composite unit.
Components of connection
Connections in steel structures
·Riveted Connections
Have you seen bridges, trains, boilers, aeroplanes, or huge structures that hold together with a button-like structure? Well, that button is called a Rivet. Riveted joints are a type of mechanical fastener that is used to join two or more pieces of material together. They consist of a series of rivets, which are inserted through holes in the material and then deformed or "set" in place to create a secure joint.
A rivet is a circular rod that is used to connect two sheet metal structures as the joints formed from these mild steel or copper rods are stronger than the welded joints and offer faster assembly.
Fig 1: Structure of Rivet
In simple terms, a riveted joint is a permanent type of fastener used to join metal plates or rolled steel sections together. These joints are extensively used in steel structures or structural works such as bridges, roof trusses, and in pressure vessels such as storage tanks & boilers.
·Bolted Connections
The bolted joint is among the most common threaded joints. They are a prime means of load transfer in machine components. The main elements of a bolted joint are a threaded fastener and a nut which prevents loosening of the bolt.
Bolted joints are widely used in construction and machine design as a means of joining parts together. This type of joint comprises of a male threaded fastener, such as a bolt, and a matching female screw thread that secures other parts in place. Tension joints and shear joints are the two primary types of bolted joint designs. While other joining methods, including welding, riveting, adhesives, press fits, pins, and keys, are also common, bolted joints are frequently used to connect materials and form mechanical structures. Essentially, a bolted joint is a combination of a fastener and a nut, with a long bolt and a nut being a typical example
Bolted Joints are defined as separable joints which are used to hold machine parts together by means of threaded fastening, i.e. bolt and nut. Since these joints are of the non-permanent variety, members can be disassembled for maintenance, inspection, and replacement without risking damage to the individual components.
Bolted Joints are significantly superior to permanent joints like welds and rivets, which cause harm to components when the components are disassembled. Applications include joining of two parts that need to be disassembled from time to time.
The bolted joints are primarily made up of two parts. It is a combination of a fastener and a nut. It consists of a long bolt with a nut on it. The bolt is inserted into the pre-drilled hole in the components, and the nut is then tightened onto the bolt's mating thread. A bolted connection is the collective term for the bolt and nut.
Threads are created by creating a helical groove on the outside of a circular shaft or hole. There is a wide range of operating environments and uses for the bolted joints. There are set standard dimensions for all these different types. This ensures that the bolted joints are interchangeable for different brands.
Figure 1: Bolted Joint Diagram
·Welded Connections
TYPES OF WELDED CONNECTIONS
The basic types of welded joints can be classified depending on the types of welds, position of welds and type of joint.
1. Based on the type of weld
Based on type of weld, welds can be classified in to fillet weld, groove weld (or butt weld), plug weld, slot weld, spot weld etc. Various types of welds are shown in Figure 15.
1.1. Groove welds (butt welds)
Groove welds (butt welds) and fillet welds are provided when the members to be joined are lined up. Groove welds are costlier since it requires edge preparation. Groove welds can be employed safely in heavily stressed members. Square butt welds are provided up to a plate thickness of 8mm only. Various types of butt welds are shown in Figure 16.
1.2. Fillet welds
Fillet welds are provided when two members to be jointed are in different planes. Since this situation occurs more frequently, fillet welds are more common than butt welds. Fillet welds are easier to make as it requires less surface preparation. Nevertheless, they are not as strong as the groove welds and cause concentration of stress. Fillet welds are preferred in lightly stressed members where stiffness rather than strength governs the design. The various types of fillet welds are shown in Figure 17.
1.3. Slot and plug welds
Slot and plug welds are used to supplement fillet welds where the required length of fillet weld cannot be achieved.
2. Based on the position of weld
Based on the position of weld, welds can be classified in to flat weld, horizontal weld, vertical weld, overhead well etc.
Based on the type of joints
Based on the type of joints, welds can be classified in to butt welded joints, lap welded joints, tee welded joints and corner welded joints.
·Bolted-Welded Connections
No. 568, Yanqing First Class Road, Jimo High-tech Zone, Qingdao City, Shandong Province, China
Copyright © 2024 Qingdao Eihe Steel Structure Group Co., Ltd. All Rights Reserved.
Links | Sitemap | RSS | XML | Privacy Policy |
Teams